
Quality Policy
To provide best quality machined products and service to our customers through our commitment by continously upgrading our process methodology and technical skills.
Quality Objective
Always to attain zero error and priority to reach precision in all our end products.
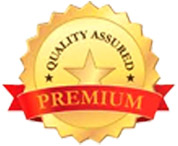
Textile Zero Sanforize Belt:
Hawa's Compressive shrinkage Rubber Belt is used to remove shrinkage of all types of fabrics. It is produced from highest quality, dirt free natural rubber and selective quality polymers to give very high compressive strength to the product. This ensures a non-sticky surface for excellent fabrics finish during shrinkage process of textile. The composition of Hawa's Rubber Belt enables extensive fabrics processing trail in Indian as well as world conditions. The high quality speciality rubber additive and high performance anti-degradants have been selected to prevent surface degradation of Rubber Belt at high temperature processing which gives excellent heat resistance and superior flex life to product.
The Rubber Belt is built on specially designed machine by skilled trained staff to give blister free product and vulcanized under controlled temperature conditions. The Rubber Belt is carefully surface ground on precision specially designed grinding machine to give smooth surface finish required for fabrics processing.
Hawa's superior quality Belt can be easily processed at high steam pressure on modern high speed machines to give shrinkage free fabrics. Because Hawa's superior heat resistance product quality gives uninterrupted service before stopping the machine for grinding the fresh smooth surface. The good abrasive surface and excellent flex quality of the Rubber Belt is expected to give atleast 10 to 15% higher meterage of fabric under ideal processing conditions than other brands of Zero Rubber Belt available in Indian market and therefore Hawa's Zero Rubber Belt is most cost competitive. Due to lower stoppage of sanforize machine for fresh surface grinding of Belt and fine surface finish after grinding, Hawa's Zero Belt has now became "First Choice" in Textile Industry.
How to Improve Life of Rubber Belt?:
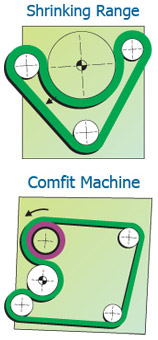
- Select proper thickness Belt for light weight and heavy weight fabrics.
- Light weight fabrics with low shrinkage : Thickness 51-55 mm for comfit process. Heavy weight fabrics with high shrinkage : Thickness 65-70 mm
- Select proper width of Belt width should be 150-200 mm wider than cloth to be processed.
- Use proper surface temperature on the Belt as needed for each type of cloth to be processed. Operative temperature on Belt surface is as low as 105 degree C and maximum 140 degree C, A correct fabric preparation and proper adjustment of moisture content of the cloth entering the surface of the Belt correct Rubber compression and proper shrinkage machine speed will permit even the most difficult fabric to be processed with optimum results at the minimum required heated cylinder temperature.
- Use the water on external surface of the Belt to keep surface temperature down. The lower end of the Belt should be pass through water tray for effective lowering Belt temperature. Also use of lubricating water supply on the Belt is squeezed at the pressure roll, the Rubber Belt must elongate and slip in order to pass through reduced nip of roller and hence inner surface of Belt must slip against pressure rollers. Use of lubricating water spray will facilitate easy squeezing of Belt will minimize inner surface at this point will considerably restrict Belt elongation, which will proportionately reduce the capacity of the Belt to pre-shrink the cloth in the wrap (length) direction.
- It is not good practice to delay Belt surface grinding. Grinding should be done periodically after checking hardness of the Belt at its side and center. If hardness differs by 3 to 5 degree shore A a proper grinding cut should be done. Preferably after running 4,00,000 meter production, surface grinding of Belt gives the Belt longer life.
- Do not neglect even small crack and grinding is recommended to prevent further damage to the Belt.
- Shrinkage machine should be cool enough before stopping the operation. Stopping machine in hot condition will reduce life of Belt drastically.
- Cleaning the Belt after fabrics shrinkage operation will extend life of the Belt. After stopping water spray, spray it with mild detergent, wipe the surface of Belt with soft brush and again start cooling water sprays to rinse all soap detergent from Belt surface. Also clean the heating drum with soft brush wash to remove any surface deposition on the drum.
- Do not use any solvent or petrol / diesel to clean Rubber Belt or metal cylinder drum.
Principles Of Zero Finish:
We explain below the compressive shrinkage principles of Rubber Belt :
The Simplest way of illustrating the principles involved in controlled Compressive Shrinking is to take a piece of Rubber and bend it as shown in Fig 1. A piece of fabric is then laid on the convex surface and held by each finger and thumb. As the Rubber is allowed to straighten, it will be seen that the length of the fabric exceeds the length of rubber, forming a loop of fabric as shown in Fig 2. This is the surplus fabric available for Compressive Shrinkage by mechanical means.
The conditioned fabric is fed on to the Rubber Belt unit at point 'A' and held firmly. At point 'B' where the Rubber Belt changes its shape from Convex to Concave, there will be a surplus of fabric, which is progressively and smoothly compressed between points 'C' and 'D'
This is a very versatile range with ability to shrink mechanically fabrics varying from light weight poplins to heaviest suiting materials up to 18%. Fabrics processed on this machine will be zero shrunk, based on the CCCT 191. A wash test with a tolerance of +1%
Request for Quote
Quality Control
The Simplest way to illustrating the principles invollved in controlled Compressive Shrinking is to take a piece of Rubber and Blend
More ››